Active anode
Gencoa have pioneered and patented the use of magnetic guidance of electrons between rotatable magnetrons and auxiliary anodes to improve process performance. Like any electrical circuit, a plasma requires a means of returning the electron current to an anode to maintain stability and uniformity.
Planar magnetrons have the surrounding dark space shield to collect the plasma electrons. A rotatable magnetron does not use a dark space shield which has lead Gencoa to develop the method to magnetically guide electrons to an effective anode – so called Active Anodes. The Active Anodes are connected to earth and use the magnetic trapping and gas injection to both guide the electrons and for gas activation.
Advantages
- Lower temperature deposition – 100% of plasma electrons collected by AA in DC discharges for 25% lower substrate heating
- AA in switching square wave dual cathode arrangements results in 30% heat reduction compared to AC power mode with AA
- Better uniformity – the electrons have a linear uniform earth return with no drift during target life
- Lower defects – the active anode reduces arcs and hence defects as a result of better plasma stability
- Higher film density – the AA produces enhanced ion bombardment of the substrate for denser films
- Harder films – eg AA doubles the hardness of sputtered carbon coatings on glass to 25 Gpa
- Lower stress – films deposited with the AA and pulsed or AC power modes present much reduced internal stress and the substrate bombardment cycles between positive and negative
- Low resistivity ITO layers as a result of the lower damage plasma – reduction of sputter voltage when anode is biased positively
AC reactive processes with Active Anodes
The AA is generally connected to the positive of the DC type power supply, or connected to earth when using switching AC type power mode. In the case of applying a positive voltage to the anode, the cathode voltage of the target can be shifted down in the same proportion as the anode voltage. This allows up to 80 volt reduction of target discharge. This is ideal for low voltage sputtering of ITO from a rotatable target. An example is shown in the video below.
AC reactive processes with Active Anodes
The use of AC power between two rotatable magnetrons is common for the high rate deposition of reactive oxide layers and other dielectric material. The addition of an earthed active anode between the two targets improves the stability of the process and hence reduces defects. Uniformity is improved as the electrons are guided to the anode without immersing the substrate in plasma.
When the film structure is analysed of the standard AC pair of cathodes and that of an anode added, the density of the layer is improved. In addition thicker layers can be deposited as the internal stress of the layer is reduced, improving adhesion to the substrate.
DC & pulsed DC non-reactive processes with Active Anodes
For a DC powered plasma, the active anode provide a long term and uniform collection of electrons that is not disturbed by substrate movement or coating of the chamber walls. Beneficial effects are in the better uniformity both down the target length and over prolonged periods of time. The AA will also reduce the temperature of the deposition as all the electrons are collected in the anode and do not contribute to additional substrate heating.
As an application example, when batch metallizing of plastic parts, outgassing of the plastic can result in a ‘semi-reactive’ type of deposition and cover the anode surface. Additionally, if HMDSO plasma activated deposition is used to seal the coated part, the chamber surfaces will become coated. Passing argon through the active anode will enable long term trouble free operation.
DC & pulsed DC reactive processes with Active Anodes
The use of pulsed DC with a reactive gas can be problematic if the resulting coating is electrically insulating – results in the ‘disappearing anode’ effect as the chamber and all parts become covered in oxide material. The Active Anode prevents this which allows any reactive process to run stably with pulsed DC power as an alternative to AC power operation. Advantages are again in the enhanced uniformity but also the use of single as well as double targets.
Gallery
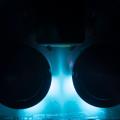
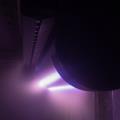
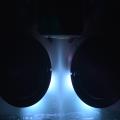
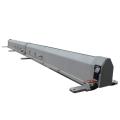
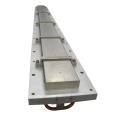
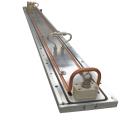
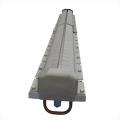
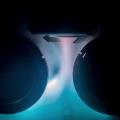
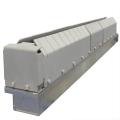
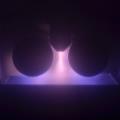
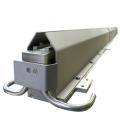
Downloads
Gencoa Active Anodes
GRS for ITO processes
Active anode flyer
SVC TechCon 2019: Controlling Sputter Processes by Optimizing Magnetic Field Guidance and System Anode Interactions
Related Applications
Perfect your process
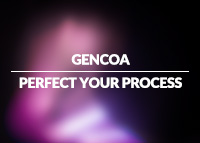
Learn more about products and services provided by Gencoa, and view a short video on the company webpage.