Optical Coatings
Optical coatings can be divided into 'large-scale' and 'small-scale'. For simplicity we associate 'precision' optics with the small scale arena, where the optical layers are typically produced to very high levels of control and uniformity over an area of up to approximately 20" (0.5m) in size. Other large scale optical effects such as window glazing and display coating are produced with lower levels of precision and will be covered in the glass coating section.
The field of precision optics covers a wide range of application areas but the optical effect can be broken down into different types:
- Anti-reflective AR, simple visible or wavelength specific
- Mirrors, metallic, dielectric, enhanced and protected
- Dichroic and polarization filters
- Spectrally selective edge filters
The common aspect of all of these types of coating is the need to create a transparent multilayer structure. Using the different layer thickness and different refractive indices of each layer, a coating structure can be built to produce the desired optical effect. Modern methods of software calculation and simulation can design the structure and optical response before the actual coating is deposited. It is a mature field in terms of optical design, however the actual layer creation is still highly demanding.
Sputtering is not the only method to create such layers, indeed a much more established method is based upon electron beam evaporation with large source to substrate distances and substrate manipulation. To provide additional energy and layer/interface smoothing plasma assist sources provide simultaneous bombardment. These e-beam methods are the traditional means of optical filter manufacture, however sputtering is now becoming more evident in a similar way to how the semiconductor industry turned to sputter deposition. Sputtering is typically used with a low (2"-10") target to substrate separation and does not usually require an additional plasma source for extra energy. To keep a sharp interface between the layers a high angle of incidence is required which leads to a 'battle' to create the very high levels of uniformity essential for such precision optical devices. There are many proprietary methods to produce such uniform layers and they generally use one or more of the following methods:
- Substrate manipulation
- 1, 2 or 3 axis
- Constant speed
- Variable speed
- Fixed or variable tilt
- Uniformity masks
- Static shaped masks
- Dynamic
- System geometry
- Source to substrate centres and relative angles
- Custom erosion profiles
Whichever method is used to create the uniformity required, the deposition of an oxide layer from a sputter source is usually performed in a reactive gas environment. To increase the rates and reduce the cycle times, the target will usually be operated in 'transition' mode. This enables the sputter yield to be high whilst the correct level of reactive gas is used to maintain the required stoichiometry. This is a highly unstable process and either a feedback gas controller is needed such as Speedflo or a very high system pumping is used to 'flatten' the hysteresis curve and generate some stability in the transition region. Gencoa are experts in magnetron design for reactive sputtering environments. Gencoa can provide a solution of each essential elements that operate in a complementary way to provide a smooth and high-rate process. The essential elements for precision optics applications include:
- Low levels of target re-deposit (or FFE for zero re-deposit)
- Low operating voltages and pressures (HS)
- Electrically floating and water-cooled anodes
- Customised erosion profiles
- Speedflo reactive gas control
- Coating uniformity simulations
- Magnetic designs for additional ion assistance
Related Products
Gencoa Newsletter
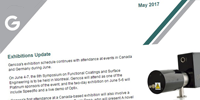
Signup to Gencoa's newsletter to receive exhibition news and updates on new product releases.