Circular VTech
Gencoa's VTech range is available for target diameters of 2" to 6" and allow the magnetic properties over the target surface to be changed by simple external adjustment, which can be performed during the process or between deposition runs.
Changes in the magnetic properties create different levels of strength and ion assistance to the coating process and allow rapid development of the thin film structures. The unique Vtech magnetron allows the variables of magnetic field properties of the source to create the following effects:
Unbalance
Variable degree of unbalance to adjust the electron release and the level of ion bombardment of the growing film.
Balance
To reduce the additional energy input to the growing film and substrate and produce low bombardment conditions.
Field Strength
To vary the magnetic field strength in order to adjust the discharge voltage and current. This can be used to compensate for the change in discharge voltage as the sputter target erodes.
Magnetic Field Shape
To adjust the magnetic field shape and therefore the interaction of the plasma with the anode in order to adjust the minimum operating pressure, striking pressure and extinguishing pressure.
The Vtech sources produce these effects by the manipulation of permanent magnets inside the magnetron head. This is done on small magnetron sources by adjusting manual verniers located on the atmosphere side of the vacuum flange, and on larger magnetrons by linear actuators via a programmable controller or PC interface. This allows instant and simple adjustment over a very wide range.
The adjustments can be performed before the coating run or dynamically during the deposition process to optimise film properties and performance. A typical example is to have high bombardment during formation of the adhesion layer and low bombardment during the bulk film deposition.
The additional advantage from a process or coating development point of view is the rapid determination of the optimum plasma and deposition conditions for specific films types. This also allows the operating envelope in terms of process parameters to attain the required films properties can be determined rapidly and gives an idea of the sensitivity of the plasma conditions to coating performance.
Gallery
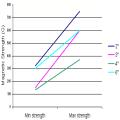
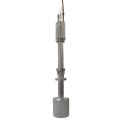
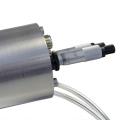
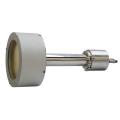
Related Applications
Gencoa Newsletter
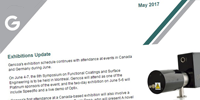
Signup to Gencoa's newsletter to receive exhibition news and updates on new product releases.